Design and performance simulation of multi-stream plate-fin heat exchangers
(一)Overview
MUSE performs detailed simulation of multi-stream plate-fin heat exchangers made from brazed aluminum, stainless steel or titanium. It can be used standalone by the thermal specialist for exchanger design or as an integrated product with AspenTech's steady-state process simulation program, HYSYS.
When used as a stand-alone program, MUSE can be used for both ‘first pass' calculations and detailed layer-by-layer analysis to evaluate new uses, revamps, process conditions and fouling cases. It can also perform full thermosyphon modeling, where one or more exchanger streams are subject to natural circulation, as well as crossflow streams.
When integrated with HYSYS, MUSE provides engineers with the ability to rigorously model processes that use multi-stream plate-fin heat exchangers, such as LNG, ethylene, or air separation. It can be used to identify capital saving opportunities in the overall process configuration. Bottlenecks can be identified, process improvements modeled for various process operating scenarios.
(二)Features
Science and Methods:MUSE is built on HTFS models and methods for plate-fin thermal-hydraulic performance. Thirty-five years of collaboration with industrial users encompassing process operators, engineering contractors and plate-fin exchanger fabricators brings unique accuracy, acceptance of prediction and validation of results.
Technical Summary:
(1)Up to 15 process streams, which can be:
- Single-phase liquids or gases, boiling liquids or condensing vapors.
- Either single components, or any mixture (with or without non-condensable gases) in any condition (superheated vapor, saturated vapor, two-phase, saturated or subcooled liquid).
- Forced flow or thermosyphon (natural circulation).
- Co-current, counter-current or crossflow.
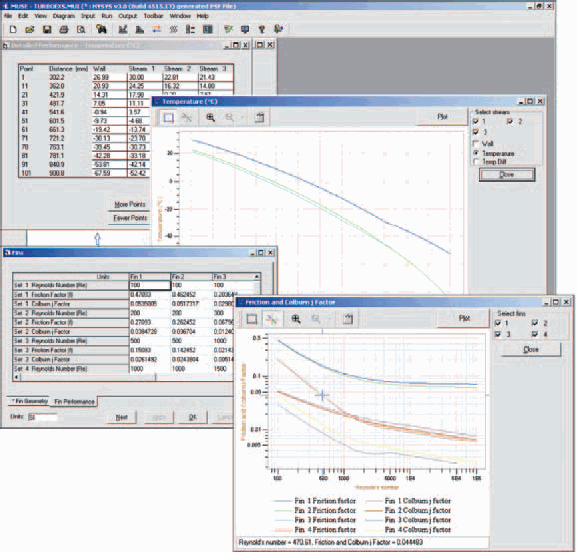
(2)Geometry
- Any complexity of exchanger inlet and outlet geometry can be modeled, including thermosyphon reboilers and crossflow geometries.
- The performance of every layer (up to a maximum of 240) can be calculated from specified inlet conditions. Metal
temperatures across the exchanger can also be predicted to enable an assessment of the layer pattern suitability.
- Single units and multiple blocks in series or parallel, with vertical or horizontal orientations can be modeled.
- Thermosyphon reboiler calculations are available for two types of reboiler, either internal (submerged in a pool of liquid) or external (connected via pipe work to the pool of liquid at the bottom of a column).
(3)Distributor Models
- Extensive pressure drop calculations for common layouts of inlet and outlet distributors, both left and right-handed versions, including twin-headed types and hardway.
- Checks for possible flow maldistribution problems.
- Redistributors, either combining or dividing and partial stream draw-off.
- These calculations include the frictional, gravitational and accelerational components of pressure change.
(4)Fin Performance Data
- The heat transfer and pressure drop performance of the finning (plain, perforated, wavy/herringbone or serrated/off-set strip) can be specified via the program input. If the manufacturers' data is not available, then research-validated fin performance correlations provided in MUSE can be used instead.
(5)Output
- Recommended 'first shot' design and summary of designs considered.
- Summary of exchanger performance.
- Temperature and quality profiles along the exchanger for all process streams.
- Comprehensive information on pressure drop through the exchanger, including details of losses in nozzles, headers and distributors.
- Fin performance data calculated by the program.
- Longitudinal thermal conduction if required.
- Detailed summary of thermosyphon calculations.
- Extensive summary of metal temperature distribution.
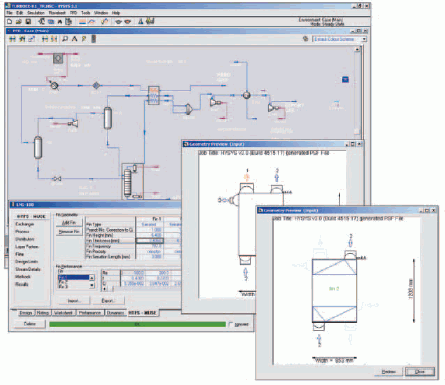
(6)Program integration
- Full implementation of the MUSE simulation user interface within HYSYS. This is augmented by the 'expert environment' of the standard MUSE user interface for first-shot design detailed graphical analysis of simulations and access to full layer analysis.
(三)Benefits
- Improved design – For design and simulation, manufacturers, engineering companies and owner operators require a robust flexible program with accurate heat transfer and pressure drop methods. MUSE provides this in a unique commercial package supported by authoritative research-based methods and validation.
- Improved process operations – Rigorous simulation of multi-stream plate-fin units allows process engineers to optimize performance of LNG, ethylene & air separation plant.
- Increased engineering efficiency – Internationally accepted MUSE simulations can be used to evaluate vendor plate-fin designs with confidence.